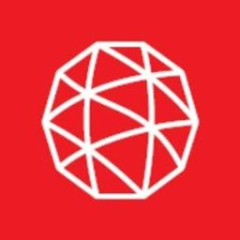
- Lean Implementation: Lead the implementation of Lean Manufacturing principles and practices across the organization. Develop and execute Lean strategies to drive process improvements, enhance productivity, and reduce operational costs.
- Value Stream Mapping: Conduct value stream mapping exercises to identify areas of waste and opportunities for improvement. Develop and implement action plans to streamline processes and eliminate non-value-added activities.
- Kaizen Events: Plan, organize, and facilitate Kaizen events (transactional and material) to engage cross-functional teams in identifying and solving operational challenges. Ensure the sustainability of improvements through follow-up and continuous monitoring.
- Training and Development: Provide training and coaching to employees at all levels on Lean methodologies, tools, and techniques. Foster a culture of continuous improvement by empowering team members to identify and implement improvement opportunities.
- Performance Metrics: Develop and track key performance indicators (KPIs) to measure the effectiveness of Lean initiatives. Analyze data to identify trends, assess progress, and make data-driven decisions.
- Problem Solving: Utilize Lean problem-solving techniques such as Root Cause Analysis, 5 Whys, and PDCA (Plan-Do-Check-Act) to address operational issues and implement effective solutions.
- Project Management: Manage continuous improvement projects from inception to completion, ensuring timely delivery and alignment with organizational goals. Collaborate with cross-functional teams to achieve project objectives.
- Change Management: Lead change management efforts to ensure smooth adoption of Lean practices. Communicate the benefits of Lean initiatives and gain buy-in from stakeholders at all levels.
- Standard Work: Develop and maintain standard work procedures to ensure consistency and best practices across the organization. Continuously review and update standard work to reflect process improvements.
- Cost Reduction: Identify and implement cost reduction opportunities through process optimization, waste elimination, and resource efficiency. Monitor and report on cost savings achieved through Lean initiatives.
- Strategic Goals: Create strategic goals in alignment with the organization's vision and objectives. Implement strategic goals set by leadership, ensuring that continuous improvement initiatives support and drive the overall strategic direction of the company.
Qualifications:
- Bachelor's degree in Engineering, Operations Management, Business Administration, or a related field. Minimum of 9 years of experience in a continuous improvement role with a strong focus on Lean Manufacturing. Graduate Degree and a minimum of 7 years of prior related experience. In lieu of a degree, minimum of 13 years of prior related experience.
- Proven track record of successfully implementing Lean methodologies and driving significant process improvements.
- Lean certification required.
- Strong analytical skills with the ability to interpret data and make data-driven decisions.
- Proficiency in data analytics tools such as Excel, Power BI, and other relevant software to analyze data, create reports, and visualize performance metrics.
- Excellent project management skills with the ability to manage multiple projects simultaneously.
- Exceptional communication and interpersonal skills, with the ability to influence and engage stakeholders at all levels.
- Proficiency in Lean tools and techniques, including value stream mapping, Kaizen, 5S, standard work, and visual management.
- Ability to work independently and as part of a team in a fast-paced, dynamic environment.
- Strong problem-solving skills and a hands-on approach to addressing operational challenges.
See more jobs in Anaheim, CA