Date: 1 day ago
City: Pasadena, Texas
Contract type: Full time
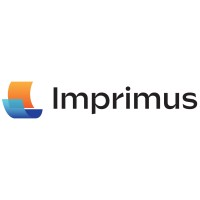
Apply
Job Type
Full-time
Description
POSITION SUMMARY: The Production Supervisor supervises shop employees in a flexo print manufacturing environment, scheduling, planning, and assigning work; implementing policies and procedures; and recommending improvements in production methods, equipment, operating procedures, and working conditions.
ESSENTIAL DUTIES AND RESPONSIBILITIES: include the following. Other duties may be assigned.
Scheduling
EQUAL OPPORTUNITY EMPLOYER: We make employment decisions based on merit and other legitimate business reasons. We aim to have the best available talent in every position. Therefore, we do not discriminate and do not permit its employees to discriminate against other employees or applicants because of race, color, creed, sex, gender, transgender status, age, sexual orientation, national origin, citizenship, ancestry, religion, marital status, military service/veteran status, physical or mental disability, genetic information, medical condition, or any other characteristic protected by local, state or federal law.
Job Type
Full-time
Description
POSITION SUMMARY: The Production Supervisor supervises shop employees in a flexo print manufacturing environment, scheduling, planning, and assigning work; implementing policies and procedures; and recommending improvements in production methods, equipment, operating procedures, and working conditions.
ESSENTIAL DUTIES AND RESPONSIBILITIES: include the following. Other duties may be assigned.
Scheduling
- Review and evaluate production tickets to ensure they can be accurately produced on press according to the provided specifications. This may include changes to estimates, product specifications, and/or work instructions to minimize errors before the schedule print date.
- Schedule production tickets to achieve maximum production efficiency and on-time delivery
- Work closely with the Shared Service Center to communicate schedule changes to customers in a timely manner.
- Facilitate and coordinate the completion of change order management forms.
- Attend daily production meetings.
- Develop improvements to reduce waste percentage and set-up times.
- Assist in troubleshooting jobs on the press.
- Manage press improvement projects.
- Facilitate conversations between the Production team to keep the department updated on improvements, challenges, or changes.
- Perform product quality checks, including proofreading and checking copy, verifying color against the PMS book or color standard, die cut quality, UPC symbol, registration, proper coating, material specification, and overall print quality.
- Assist the production department in inspecting and sampling at various stages of the work process.
- Review quality documents and retain samples daily to ensure product quality and compliance with procedures.
- Ensure the team follows the work instructions for achieving good quality, including line clearance, color management, and ink adhesion tests.
- Perform customer-specific quality verification tests (adhesion tests, spectro analysis, etc).
- Perform production approval checks.
- Enter quality incidents into the tracking system and distribute them for investigation and response.
- Assist in recording and investigating internal quality incidents (set aside items, reruns, shortages)
- Assist in investigating external quality incidents and create corrective action documentation/reports for senior management to review.
- Segregate and review questionable products regarding non-conformance issues.
- Assist in monitoring incoming RMA shipments and coordinating the investigation/disposition of material.
- A High School Diploma or GED is required. A degree in Business Management or Administration, or equivalent knowledge and experience, is preferred.
- Requires 3+ years of previous lead experience in a flexographic printing environment, plus five years of flexographic printing experience.
- Must have experience in manufacturing processes, procedures, and techniques, quality systems, and standards.
- Must know machines, tools, technology, business, management practices, and principles.
- 2+ years of experience using Microsoft Office software (Outlook, Excel, and Word) and the ability to learn specialized software programs (Label Traxx).
- Reduction in safety incidents.
- Reduction in production-related quality occurrence.
- Continuous improvement in uptime in production.
- Continuous improvement in safety
- Communication with internal and external customers is timely.
- Communication with employees is effective.
- A positive attitude is demonstrated to both internal and external customers.
- Employee counseling statements have been considered training and have resolved past performance issues.
- Meeting lead time and on-time delivery targets.
EQUAL OPPORTUNITY EMPLOYER: We make employment decisions based on merit and other legitimate business reasons. We aim to have the best available talent in every position. Therefore, we do not discriminate and do not permit its employees to discriminate against other employees or applicants because of race, color, creed, sex, gender, transgender status, age, sexual orientation, national origin, citizenship, ancestry, religion, marital status, military service/veteran status, physical or mental disability, genetic information, medical condition, or any other characteristic protected by local, state or federal law.
See more jobs in Pasadena, TX